Introduction
Warehouse technology is rapidly advancing, and has been adopted heavily in retail distribution centers including Amazon, Target, and Walmart. Amazon specifically values automation so highly that they acquired Kiva Systems, now branded as Amazon Robotics, for $775M. However, motor vehicle OEMs have been slow to invest in and adapt to new warehouse technology. Factors unique to the OEM business, including challenging part dimensions and characteristics, stringent customer requirements, and fluctuating volumes, make technology decisions more complex.
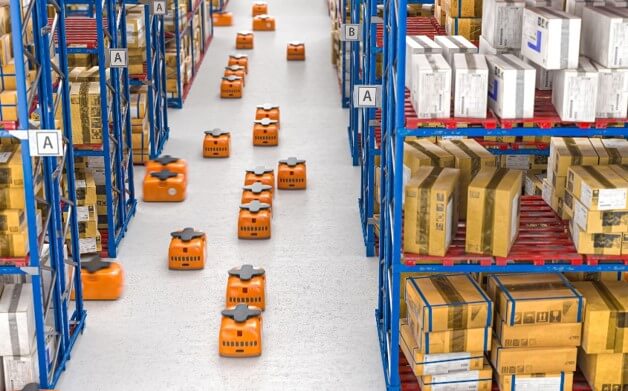
While there are challenges, there is also increasing opportunity and need for OEMs to adopt new technology. The next decade will bring additional requirements and challenges, driven by factors such as sales growth, expansion of e-commerce, and more demanding customer requirements. A continued push for vehicle uptime, driven by customer demand and increasingly complex inventory planning systems, will require parts to be delivered in shorter response cycles and in small quantities. By pairing “classic” warehousing best practices with the right technology, OEMs can position themselves to excel in future business environments.
In this article, Carlisle shares examples of different warehouse technologies and highlights their benefits and use cases. Carlisle also provides a framework for meaningful technology evaluation and implementation, to help motor vehicle OEMs select the appropriate technology based on their operational improvement goals.
Available Technologies
Warehouse technology addresses nearly every function and aspect of the business; the sheer quantity of solutions can be overwhelming. These solutions fit within the broad categories of storage, information, movement, and packing technology. In order to best assess technologies, Carlisle recommends comparing technology based on their functional characteristics and benefits.
Storage Technology
Storage technology aims to optimize space utilization by achieving greater storage density, while reducing damage through proper and safe storage techniques. Many facilities choose automated storage and retrieval systems (ASRS) to automate putaway, storage, and picking functions within one system. OEMs often implement and use ASRS in central distribution centers, where high part number counts and slow part movement make storage density a key focus.
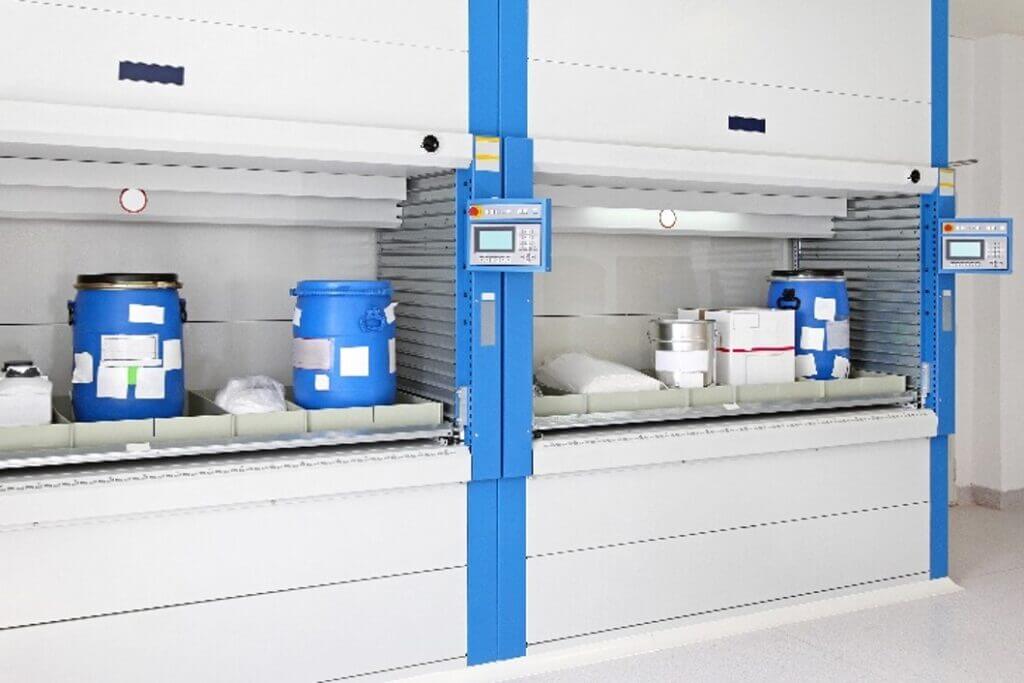
There are two main types of ASRS solutions, with derivatives of each: (1) shuttle systems and (2) adjusting shelf systems. Shuttle systems use guided shuttles to transport totes or bins from racking locations to an operator at a pick station outside of the racking. The operator picks the appropriate number of parts from the tote/bin, then the shuttle puts the tote/bin back into the racking. Traditionally, these shuttles run along normal racking, however, cube storage systems have become available more recently. These are modular cube structures that house parts within them with extreme density, stored in ways that are not accessible to a human. Similar to the traditional shuttle system, there are operator pick stations along the edge of the cube where bins are delivered from within the cube.
Adjusting shelf system technology is comprised of vertically rotating shelves that move up and down to an operator at a work station to allow the operator to pick parts from the shelf. Adjusting shelf systems make better use of vertical space. While both shuttle systems and adjusting shelves provide better space utilization, higher quality, and reduced operator movement, it is important to deploy them in the appropriate warehouse zones. Shuttle systems are used with pallets and totes, while automatically adjusting shelves are best suited for small part bin storage.
Information Technology
Information technology in warehousing automates the gathering, tracking, management, and display of data within the facility. These solutions include robotic process automation, augmented reality, and drones.
Robotic process automation (RPA) is a script run to standardize a process, typically on a computer. Similar to an Excel macro, RPA is used across a wide range of applications to increase efficiency and productivity. It is best used to perform highly repetitive tasks with little variability. Examples of RPA use include automating common customer response emails, selecting a transportation mode based on a set of rules, or automating reporting that requires data pulls from multiple systems or multiple user interactions. RPA can be developed in-house; however when outsourced, third parties commonly offer both use case identification and implementation support.
Augmented reality is an interactive experience of a real-world environment enhanced by computer-generated perceptual information. Warehousing applications commonly use computerized glasses that display key information in the operator’s field of vision, such as locations, SKU numbers, and part quantities. The technology drives quality improvements through process verification, alerting the operator if a mistake has occurred during putaway sorting, picking, or shipment consolidation. Though OEMs and 3PLs have begun piloting augmented reality in select locations, adoption is still not widespread.
Drones are typically used for inventory management data collection, as they perform cycle counts quickly and accurately, eliminating the need for manual counting. This drives improved productivity and quality, while also removing potential safety risks such as manual cycle counts at high rack locations. Drone inventory counts are often conducted at night to reduce man/machine crossover and save time to conduct other activities during the day. Drones are most applicable in highly palletized facilities where they can count very efficiently, but are less effective in warehouses that house many small parts. Aerial drones can also interact with RFID-tagged trailers to continuously monitor yard inventory, real-time trailer location, and dwell times. Currently, drones do not have the payload capacity to carry parts around the warehouse, but it is likely that this may be a future development.
Movement Technology
Movement technology automates or assists the physical movement of parts within the warehouse. This technology ranges from basic solutions, such as conveyor belts, to autonomous technologies, such as self-driving material handling equipment and automated mobile robotics.
Self-driving material handling equipment (MHE) drive along pre-planned paths in the warehouse, shuttling parts while they drive. Autonomous forklifts and tuggers are the most common types of MHE. Tuggers are best used to move parts from receiving to a putaway buffer area in racking, or from a buffer in racking to an outbound packaging area. Autonomous forklifts may be used to execute repetitive pick tasks. The main benefits of self-driving MHEs include reducing human travel and man/machine crossover, providing both cost and safety benefits.
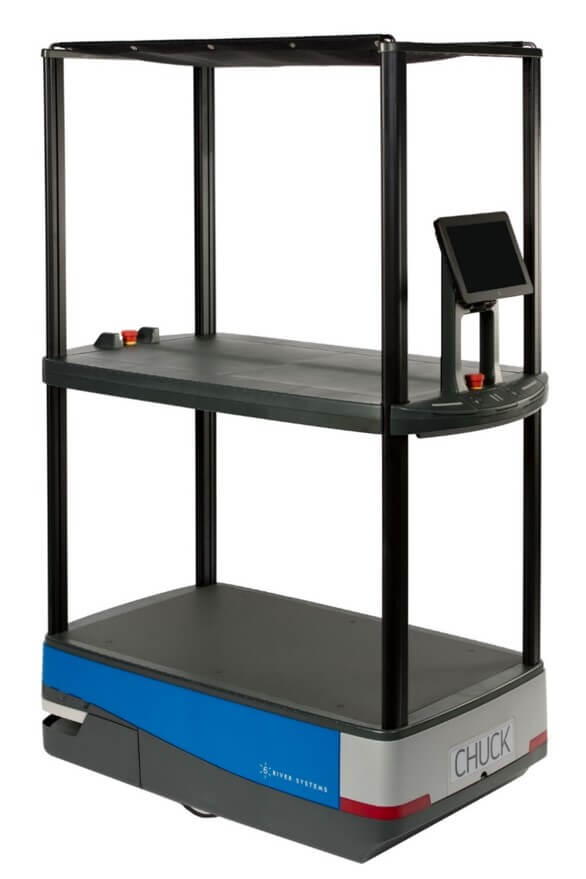
Automated mobile robots (AMRs) are a form of self-driving technology that has rapidly developed over the past few years. AMRs are easy to implement and offer benefits of increased productivity, reduced walking, and better ergonomics for human operators. These robots typically operate as self-driving pick trolleys that use cameras and LIDAR (method for measuring distances by illuminating the target with laser light and measuring the reflection with a radar sensor), to “see” their surroundings and either lead, follow, or be picked/passed by operators.
Leading AMRs bring operators to a pick location, whereas following AMRs follow an operator to a pick location. Pick and pass AMRs are not assigned to a single picker. Instead, pickers are stationed in dedicated zones and bots await interaction from a picker. The bot then moves onto the next picker in the zone, effectively carrying multiple orders. When an AMR has been filled to capacity, it self-directs to a pack area for unloading, once again reducing human walking distance. AMRs are also used for inbound putaway, functioning in a similar manner as outbound picking.
Packing Technology
Packing technology automates or assists inbound and outbound packing activities in the warehouse. OEMs have used technology such as automated baggers and taping machines to accomplish simple, repetitive tasks for years. More advanced packing technologies, such as automated box creation and dimensioning systems, have had less adoption in the motor vehicle industry to date.
Automated box creation systems can create boxes and pack parts at very high speeds. Advanced versions are used in retail warehouses where parts are fed into the system and custom boxes are built around the parts or an entire order. This can reduce material costs, increase box and truck cube utilization, and increase the productivity of packing. However, there have been reports of downtime issues as a result of hot glue jams.
Another example of packing technology is a dimensioning system. When used to audit shipments, these systems can automate measurement and weighing tasks, resulting in improved manifesting, shipping cost savings, and revenue recovery. More accurate part data can improve overall warehouse slotting and storage as well.
Technology Evaluation, Selection, and Implementation
Selecting the appropriate warehouse technology can be a daunting task. Carlisle recommends first identifying the area of opportunity in your facility or network – Is the goal to increase productivity? Quality? Optimize space and storage? After identifying goals and desired outcomes, OEMs should begin narrowing down technology options through high-level filtering. This can be accomplished via simple ‘yes’ or ‘no’ questions regarding factors such as benefits, downtime, flexibility, maturity of technology, and process and system integration. The goal of this exercise is to prioritize technologies to quickly identify those clearly unsuitable for the operation, and those that may achieve intended goals.
After narrowing the options, OEMs should assess technologies through a rigorous evaluation process. Three main attributes for each piece of technology should be considered – (1) benefits, (2) implementation/ease of use, and (3) risks/drawbacks. Each attribute holds a number of considerations which OEMs should explore and adapt to their specific business needs – benefit sub-components focus on KPI improvement; implementation considers the level of integration and use over time; risks evaluate the overall monetary investment and potential for downtime.
Benefits Evaluation Criteria
- Productivity
- Quality
- Inventory Accuracy
- Safety & Ergonomics
- Space Utilization
Implementation Evaluation Criteria
- Flexibility
- Scalability
- Maturity of Technology
- Process Integration
- System Integration
Risks Evaluation Criteria
- Upfront Cost
- Ongoing Support Requirements
- Machine Down Effect
- Machine Down Frequency
- Space Consumption
Once technologies have been selected, a four-step approach to implementation should be used: (1) plan, (2) pilot, (3) evaluate and revise, and (4) implement.
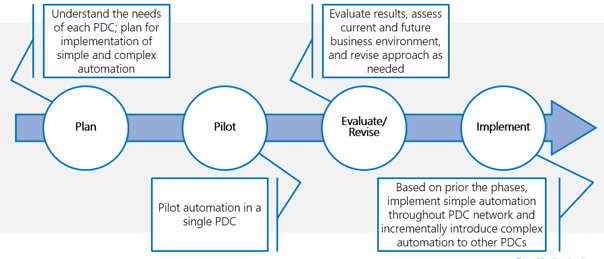
Initial planning includes need identification, technology evaluation, and business case development. After planning, OEMs should look to pilot technology in a single PDC. The length of the piloting phase will often depend on the complexity of the solution. For less complicated solutions such as an auto bagging machine, a few weeks of piloting is likely sufficient. However, more advanced technology, such as an AMR, need for several months of piloting at minimum. Once piloting is complete, OEMs need to evaluate results and revise based on findings. This involves determining if the technology met expectations, addressing any unintended consequences, and identifying additional changes to be made. Finally, OEMs should consider network-wide implementation. A site-by-site rollout is ideal for complex solutions, while a simultaneous rollout works for simple machinery. It is important to have strong outputs from the prior phase to ensure that the technology and associated processes drive expected results in different PDCs.
Authors
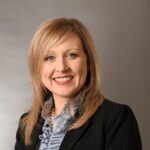
Amy Marzonie
Director
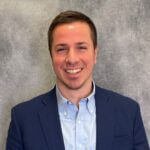
Eric Francucci
Manager
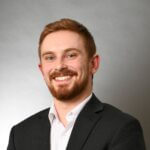
Hunter Roberts
Senior Consultant