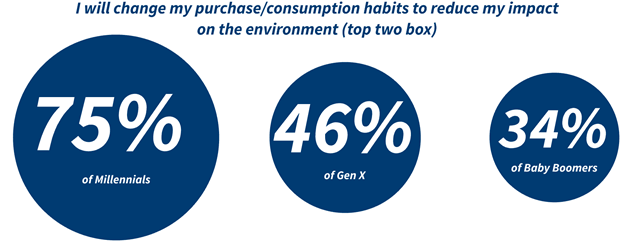
With OEMs including Ford, GM, Volvo Cars, taking action and establishing sustainability pledges, others cannot turn a blind eye to the importance of establishing sustainable practices or they risk falling behind. The motor vehicle industry is extremely competitive, and the battle over market share is always a top talking point among executives. OEMs can’t risk losing a single customer, which today means competing on sustainability as they compete on product, technology, finance, service, and every other aspect of the business.
Many OEMs’ sustainability commitments clearly communicate their goals to potential customers. We’ve all heard the broad-scale goals such as:
- Achieve carbon neutrality by 2050
- Attain zero emissions from our vehicles and facilities
- Use 100 percent local, renewable electricity in all manufacturing by 2035
These goals are good because they’re measurable. For example, 100 percent local, renewable energy is easily measured, and progress can be tracked. The goals also have a time limit – by 2035, or by 2050. This four-part series will broaden beyond these stated goals, and an OEM that follows our framework will see gains in carbon neutrality, decreased emissions, and an increase in local, renewable energy – among many other things.
Defining Sustainability
Sustainability is our preferred phrase to describe a variety of environmentally friendly missions. Sustainability means that people and companies act to preserve our ecosystem. As you’ll see, the ecosystem is environmental – but it’s also social. Sustainable supply chains (the focus of this series) need to be designed around our world and our people.
As this series progresses, we’ll get more tangible. We reviewed 30+ journal articles, company sustainability goals, mission statements, and other documents to come up with a comprehensive list of all the elements that people refer to when they say “sustainability.” From here, you’ll read:
- What are the key drivers of sustainability?
- These are broad categories we use to help us think about the problem
- What are the “core KPIs” of sustainability?
- These are the specific metrics and numbers that companies use or track when they state their goals and progress
- How do companies actually make sustainable decisions?
- We’ll share one (of many) way to evaluate tradeoffs between a sustainable yet expensive option and a more traditional but cheaper option
- What are some specific actions that supply chains (in particular, aftersales supply chains) can take today?
- We have case studies where companies have opted to make sustainability-driven decisions
By the end of this series, you’ll understand the drivers of sustainability, the KPIs that measure performance in related to each driver, and a decision framework for supply chain strategy built with sustainability as a core tenant. And you’ll leave with some examples you can immediately create business cases around.
Drivers of Sustainability
In our literature review, we identified dozens of different ways to measure sustainability, ranging from “carbon emissions” to “noise pollution.” These are all good, but they’re not organized in a way that allows us to categorize and make decisions. So, we’ve categorized them all into five groups for you. It’s important to note these are categories, not metrics – metrics come in our next post.
Raw materials, energy, human costs, reclamation, and water are the key drivers of sustainability. Understanding what each driver is, and how it relates to the processes inherent to aftersales, will enable discussions of sustainability within the supply chain. We’ll describe each category before moving into more detail.
Raw materials are the building blocks of production. They include iron, aluminum, lithium, cobalt, oil, wood – we could go on but we’d end up listing every element on the periodic table. Concern with sustainability of raw materials is multi-faceted.
- Some raw materials are non-renewable. Being dependent on a non-renewable resource is a step away from sustainability
- Raw material acquisition can be damaging to the environment. Heavy mining operations disrupt the environment and habitats of plants and animals
Energy is the driving force of production, and emissions are the detrimental byproduct. Our goal is to maximize our energy utility while minimizing our waste, efficiency is key in manufacturing. Here’s a tricky example. We know coal energy is very inefficient, capturing roughly 33% of the energy generated from the burning process[1]. This doesn’t include the energy and damage done in the extraction process. Meanwhile wind energy retains roughly 50% of the energy generated by the wind moving the rotor[2]. This means wind energy is more “fuel efficient” than coal.
But wind energy is nearly infinitely more sustainable. This is because the source – the actual coal – when burnt, releases tons of carbon dioxide into the atmosphere. Wind power does not. Emissions are what we ultimately care about – if all energy use was from renewable sources that produced zero carbon, we’d be in a much better environmental situation.
There are two ways to be more sustainable when using energy.
- Use less energy – this is the ultimate goal
- Get energy from a more sustainable source, like wind, hydroelectric, geothermal, or solar power. These are often called renewable resources. This is reflected in many OEMs’ commitments to use local, renewable energy
Water is essential to industrial processes such as cleaning, cooling, and many other tasks. While water is replenished by nature, the rate of clean water use by humans outpaces the rate of replenishment[3]. It is both important for the environment, and profitability of a business, to optimize water usage.
Reclamation, within the scope of this series, refers to any repurposing of land, waste, or materials into a useful state. Efficient reclamation processes can reduce cost while improving public perception of a brand. Some examples include:
- Restoring mined land to a usable state for the local community
- Utilizing recycled products in the manufacturing process
- Converting process by-products into inputs for other processes – this applies to aftersales
Human costs refer to the cost the community, whether global or local, faces, as a result of the manufacturing process. Air pollution, noise pollution, and degradation of land all impact the community. Degradation of land could lead to increased probability of natural disaster, which could disrupt the supply chain and extend lead times to aftersales distributors.
Every physical process (and some non-physical processes as well) have human costs. Some are more severe than others. For example, risky mining operations with poor safety records have a higher human cost than an activity like trucking which is endemic to aftersales. Truckers tend to have poorer health outcomes than the average American. This is human cost. Human costs are even harder to quantify than the other four categories, but since our definition of sustainability includes the entire ecosystem, we can’t ignore people entirely.
In Our Next Post…
We’ve shared our perspectives and insights into WHAT sustainability is, in the context of aftersales, particularly in the context of supply chains. We also shared our groupings into the KEY DRIVERS of sustainability. In the next segment of this four-part series, we will dig deeper into the metrics of sustainability – once we understand how to measure sustainability, we can determine how to effectively track and address sustainability initiatives in the supply chain.
[1] https://www.ge.com/power/transform/article.transform.articles.2018.mar.come-hele-or-high-water#
[2] https://css.umich.edu/factsheets/wind-energy-factsheet
[3] https://www.fmamfg.org/blog/water-reuse-recycling-conservation-manufacturing
Authors
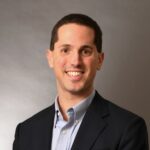
Nate Chenenko
Director